1.2. Закономірності зміни технічного стану машин
1.2.1. Параметри технічного стану машин та їх
перехід із справного в непрацездатний стан
1.2.2. Фактори, що спричиняють несправності
машин
1.2.3. Заходи, які запобігають інтенсивному
спрацюванню
Про зміну технічного стану об'єкта судять за значеннями діагностичних
(контрольованих) параметрів, які отримують у процесі технічного
діагностування.
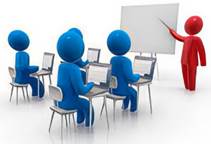
|
Розрізняють прямі і непрямі діагностичні (контрольовані) параметри.
|
До прямих параметрів
відносять:
•
спрацювання поверхні деталі;
•
зазор у з'єднанні спряження деталей;
•
люфт та ін.
|
До непрямих параметрів
відносять:
• тиск
оливи в головній масляній магістралі двигуна;
•
вміст CO у вихлопних газах двигуна;
•
шум під час роботи механізмів машини;
•
вібрація;
•
температура охолоджувальної рідини двигуна тощо.
|
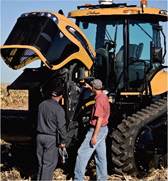
|
|
|
|
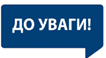
|
У межах технічного ресурсу (упродовж амортизаційного
періоду) деталі і спряження машин поділяють за розмірами, відхиленнями від
геометричної форми та зазорами і натягами на нормальні (заводські), допустимі
та граничні параметри.
|
Нормальні ‒ встановлює завод-виробник на підставі вимог, що
визначаються умовами роботи машин, вони відповідають робочим кресленням.
Допустимі ‒ це ті параметри, за яких деталі або спряження
будуть придатні до роботи (експлуатації) упродовж наступного міжремонтного
періоду.
Граничні ‒ це параметри, за досягненні яких порушується
нормальна робота з'єднання,
механізму, складальної одиниці, машини. Можлива раптова відмова (аварія). Під час аварійних
зношуваннях експлуатація деталей не припустима.
|
Хід процесу зношування в часі має вигляд кривої щодо
залежності зносу U від часу t (рис. 1.4).
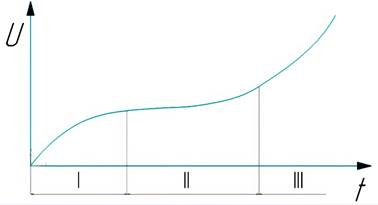
|
Рис. 1.4.
Залежність зносу від тривалості (обсягу робіт):
I – стадія припрацювання; II – стадія нормальної роботи;
III – стадія аварійного зношування
|
Як видно з рисунка зношування відбувається у три стадії
(періоди):
На І стадії
здійснюється припрацювання контактуючих поверхонь деталей (графік наводить
зміни зносу тільки однієї з поверхонь). Ця стадія характеризується
нестабільністю параметрів тертя, початковою високою швидкістю зношування dU/dt, що обумовлено значними
пластичними деформаціями нерівностей поверхневих шарів деталей, перебудовою
технологічного мікрорельєфу поверхонь на експлуатаційний та зміною
фізико-механічних властивостей.
Найтривалішою
є II стадія. Ця ділянка кривої відповідає періоду роботи з'єднання після
припрацювання. Під час нормальної роботи спостерігається стабілізація
параметрів тертя, швидкість зношування невелика і орієнтовно однакова і
стала.
Знос деталей
може призвести до погіршення умов тертя під час роботи з'єднань, у результаті
чого швидкість зношування різко зростає. Цей період процесу зношування
відповідає кривій на стадії III.
Криві зміни
зносу в часі, залежно від умов роботи деталей (виду, з'єднання,
фізико-механічних властивостей поверхонь тощо), можуть мати не всі три стадії
вихідної (класичної) кривої, а дві або одну (рис. 1.5).
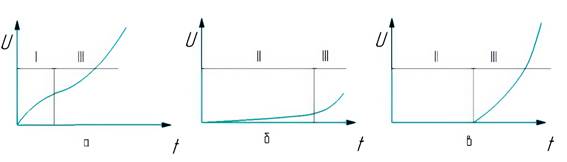
|
Рис. 1.5.
Криві зміни зносу в часі залежно від умов роботи деталей:
а – відсутня стадія нормальної роботи;
б, в – відсутня
стадія припрацювання
|
Уявлення законів
зношування в аналітичній формі – складне завдання і перебуває в процесі
становлення.
Незважаючи на складність і різноманітність процесів, що впливають на
знос поверхонь, є основні, які переважають у конкретних умовах тертя. Вони
визначають вид зношування і характер зносу поверхонь. Так, за ДСТУ 2823, для
уніфікації уяви про основні процеси під час зношування їх класифікують на три
основні групи (табл. 1.1).
Таблиця 1.1
Групи зношування
Ознака зношування
|
Вид зношування
|
Механічне зношування
|
Абразивне, гідро-,газоабразивне,
гідро-,газо- ерозійне, кавітаційне, утомне, фретингове,
адгезійне
|
Механіко-хімічне зношування
|
Окиснювальне,
фретинг корозійне
|
Від дії електричного струму
|
Електроерозійне
|
Таблиця 1.2
Приклади прямих параметрів (зносу)
деталей і спряжень машин
Вид зношування
|
Приклад зносу
|
Механічне
зношування – це стирання (диспергування)
і зминання (пластична деформація) контактуючих поверхонь під час їх
відносного переміщення. Під час відносного переміщення поверхонь тертя
мікронерівності зрізаються і видаляються. Зношуванню поверхонь тертя сприяє
їх різна твердість, внаслідок чого твердіші складові врізаються у менш
тверді.
|
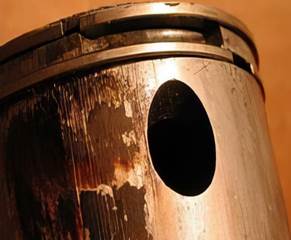
Рис. 1.6. Механічне
зношування поршня
|
Зминання ‒ це наслідок дії тертя і
підвищення при цьому температури, під час яких окремі нерівності пластично деформуються. Водночас можуть виникати
молекулярні взаємодії, внаслідок чого відбувається виривання матеріалу в
місцях охоплення. Охоплення характеризується глибинним вириванням
матеріалу, перенесенням його з однієї поверхні на іншу, внаслідок чого
виникає заїдання або заклинювання від одночасної дії механічних і
молекулярних сил тертя. Це зношування називається молекулярно-механічним.
|

Рис. 1.7. Заклинювання механізму внаслідок дії тертя і підвищення при
цьому температури
|
Абразивне зношування відбувається внаслідок зскрібання з поверхні деталі частинок металу,
дії на її поверхню твердих частинок, занесених у зону тертя потоком рідини,
повітря або газу, а також безпосереднього контактування з абразивним
середовищем (робочі органи сільськогосподарських машин, ходові частини
гусеничних машин тощо).
|
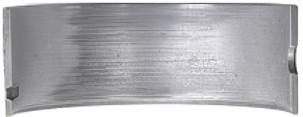
Рис. 1.8. Абразивне зношування
підшипника (вкладиша) під дією твердих частинок, занесених у зону тертя
потоком масла
|
Корозійне зношування відбувається без тертя, внаслідок взаємодії металу з киснем повітря,
атмосферною вологою і хімічно активним середовищем та під час контакту двох
різних металів. На незахищених від атмосферної вологи поверхнях деталей
машин утворюється плівка окислів ‒ іржа, яка знижує фізико-хімічні
властивості металу й призводить до прискореного руйнування поверхні деталі.
|
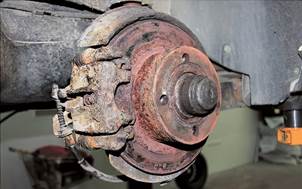
Рис. 1.9. Корозія кронштейна супорта внаслідок
взаємодії металу з киснем повітря, атмосферною вологою і хімічно активним
середовищем
|
Окислювальне зношування відбувається під час тертя ковзання і кочення (в підшипниках). На
початковій стадії зношування окислення відбувається у поверхневих шарах, у
другій стадії воно поширюється на всю глибину шару пластичної деформації. У
першій стадії зношування на поверхнях тертьових деталей утворюються тверді
розчини кисню в металі, у другій стадії ‒ хімічні сполучення кисню з
металом, внаслідок чого структура поверхневого шару значно змінюється і під
силою тертя викришується.
|
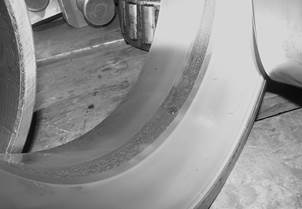
Рис. 1.10. Окислювальне зношування
бігової доріжки конічного роликового підшипника
|
Теплове зношування відбувається під дією тепла, що утворюється внаслідок тертя поверхонь
під час великих швидкостей ковзання і великих тисках. Структура металу
ділянок деталей, що знаходяться в зоні високих температур, з часом
погіршується, стає більш крупнозернистою, виникають мікроскопічні тріщини й
окислення його структурних складових. Тепловому зношуванню підлягають днища
поршнів, клапани, деталі топок машин для приготування кормів тощо.
|
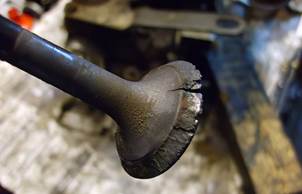
Рис. 1.11. Теплове зношування
тарілки клапана
|
Кавітаційне зношування відбувається від багаторазових ударів рідини у поверхні деталі у вигляді
кумулятивних струменів, що рухаються з великою швидкістю. Ці струмені
виникають під час закривання бульбашок, що утворюються на поверхні деталі
внаслідок вібрації останніх або після розриву потоку рідини, багаторазові
удари струменів рідини по одному й тому ж місцю металу призводять до його
місцевого руйнування й утворення заглибин або наскрізних отворів (лопат і
корпусів відцентрових насосів).
|
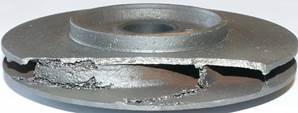
Рис. 1.12. Кавітаційне зношування
робочого колеса відцентрового насоса
|
Електроерозійне зношування відбувається від проскакування електричних іскрових зарядів із однієї
частини деталі на іншу, які мають вибуховий характер, під час якого
відбувається виривання частинок металу й перенесення його з аноду на
поверхню катоду. До таких деталей належать електроди свічок запалювання,
контакти переривників-розподільників, щітки і колектори стартерів тощо.
|
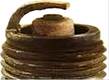
|
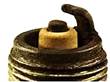
|
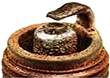
|
Рис. 1.13.
Електроерозійне зношування електродів свічок запалювання
|
Зношування від утомленості виникає внаслідок дії знакозмінних або циклічних навантажень, які
перевищують границю плинності поверхневих шарів металу. На поверхні
утворюються мікро- і макротріщини, а також віспоподібні заглибини, що вини-кають внаслідок
викришування частинок металу з поверхонь тертя в місцях концентрації
знакозмінних або пульсуючих напружень. Цей вид зношування характерний для
шарикових і роликових підшипників, зубців шестерень та інших подібних за
умовами роботи деталі.
|
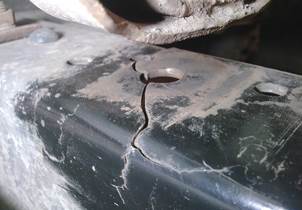
Рис. 1.14. Зношування металу від
утомленості
|
Зношування під час фретингу відбувається на спряжених
поверхнях в умовах складного динамічного навантаження під час невеликих
коливальних відносних і зворотно-поступальних переміщеннях ‒ складний
вид деформації. Цього виду зношування зазнають шестерні, шліци валів,
посадочні поверхні підшипників кочення, отвори під підшипники, послаблені
болтові та заклепочні з'єднання рам та ін.
|
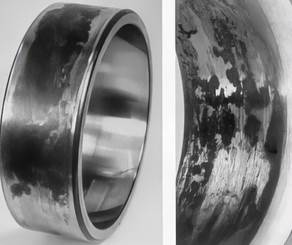
Рис. 1.15. Контактна фретинг-корозія підшипників
|
Методи
визначення зношування деталей:
• метод мікрометричного вимірювання;
• методи зважування;
• метод штучних баз;
• метод радіоактивних ізотопів;
• метод хімічного аналізу оливи.
Останні три
методи відносяться до посереднього визначення зношування деталей.
Таблиця 1.3
Приклади методів визначення зношування деталей
Метод визначення
|
Приклад визначення
|
Метод
мікрометричного вимірювання – один з найпростіших
і широко розповсюджених прийомів визначення зношування деталей. Водночас
потрібний розмір деталі визначається вимірюванням за допомогою
штангенциркулів, мікрометрів, індикаторних приладів до і після досліду. За
різницею розмірів роблять висновок про лінійне зношування. Для визначення
досить малих зношувань (наприклад, у прецизійних парах і деталях:
плунжерах, нагнітальних клапанах, золотниках гідросистем та ін.)
використовують профілографи.
|
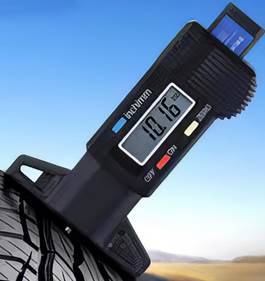
Рис. 1.16. Вимірювання глибини рисунка протектора шини електронним
штангенглибиноміром
|
Метод
зважування – широко використовується для визначення зношування деталей
у лабораторних умовах. Знос визначають за зміною маси зразка до і після
досліду. Цей метод неможливо застосовувати, якщо основним видом зношування
є пластична деформація поверхневих шарів матеріалу деталі.
|
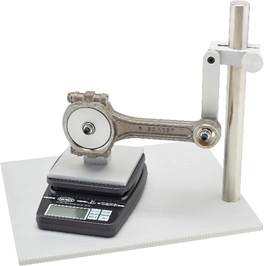
Рис. 1.17. Зважування шатуна на вагах лабораторних
|
Метод штучних баз – метод
вимірювання відбитків і метод вимірювання вирізаних заглибин. Сутність
методу відбитків полягає в тому, що
на досліджуваній поверхні в крапці, що цікавить, наноситься відбиток за
допомогою спеціального приладу в вигляді піраміди або конуса. Вимір довжини
діагоналі основи піраміди або діаметра основи конуса роблять за допомогою
оптичного пристрою. У разі використання методу вирізаних заглибин на поверхні тертя за допомогою
спеціального інструменту вирізають заглибину із заздалегідь заданим
геометричним профілем. За зміною її глибини визначають величину лінійного
зносу. Метод вирізняється високою точністю.
|
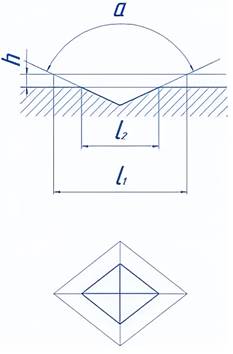
Рис. 1.18. Метод штучних баз
|
Метод радіоактивних ізотопів – ґрунтується на вимірюванні кількості
радіоактивної речовини в оливі за допомогою спеціального лічильника. За
зміною кількості цієї речовини робиться висновок щодо збільшення зносу
деталі. Радіоактивна речовина (ізотопи вольфраму, сурми, кобальту тощо)
вводяться в деталь під час її відливання, гальванічного нарощування,
дифузійного насичування та ін.
|
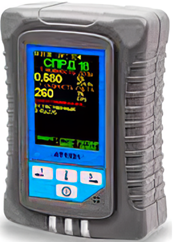
Рис. 1.19. Спектрометр МКГ-АТ1321
АТОМТЕХ (ідентифікація радіонуклідів, ізотопів)
|
Метод хімічного аналізу оливи – використовується для визначення зносу
деталей двигуна внутрішнього згоряння й інших складних одиниць. За
кількістю заліза та інших продуктів спрацювання у оливі робиться висновок
щодо величини зношування за певний встановлений час.
|
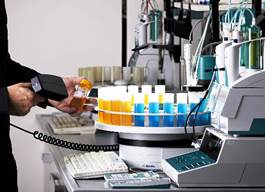
Рис. 1.20. Лабораторне обладнання для
хімічного аналізу оливи
|
Перевага двох
останніх методів у тому, що для визначення зношування немає необхідності
вдаватись до розбирання машин.
Проте, метод
визначення кількості заліза в оливі дає сумарне зношування усіх спряжень
деталей, а не кожної окремо. Практично під час визначення технічного стану
складної одиниці часто застосовують діагностичні
методи виявлення зношування. Наприклад, зношування плунжерної пари
можна визначити за станом герметичності, а зношування деталі форсунки ‒ за зменшенням тиску і погіршенням якості впорскування
палива та ін.
Різні за
характером види спрацювань деталей служать передумовою виникнення
несправностей елементів будови машин.
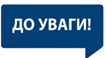
|
Фактори, які служать передумовою виникнення
несправностей:
|
•
несвоєчасне проведення технічного обслуговування (ТО);
•
застосування невідповідних експлуатаційних матеріалів;
• низький
рівень кваліфікації обслуговуючого персоналу;
•
порушення правил експлуатації машин тощо.
|
З часом, у
машини, яка виконує будь-яку роботу, зменшується потужність, тягове зусилля,
продуктивність та економічність, збільшується витрата паливо-мастильних
матеріалів, час на виконання робіт, погіршується якість їх виконання.
Головною причиною цього є спрацювання
деталей, яке призводить до
зміни їх розмірів та форми, а також взаємного розміщення у механізмі.
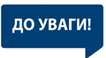
|
Грамотна експлуатація, раціональне використання,
вчасне і якісне обслуговування, ремонт та правильне зберігання сприяють
підтриманню експлуатаційних показників машин у встановлених межах.
Отже, управління технічним станом машин полягає в:
|
•
обґрунтуванні та у призначенні видів і періодичності ТО;
•
призначенні видів і методів ремонту;
•
критеріях граничного стану;
•
ступені відновлення технічного ресурсу складових частин;
•
тривалості використання машини до списання.
Перехід
машин зі справного стану в непрацездатний стан є результатом проявлення
дефекту.
|
Дефектом називають кожну окрему невідповідність об’єкта
встановленим вимогам. Зокрема, під дефектом деталі розуміють кожне окреме
відхилення її параметрів від величини, яка установлена технічними умовами або
робочим рисунком. Водночас перехід машин з одного стану в інший відбувається
внаслідок пошкодження або відмови.
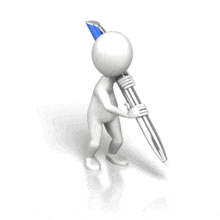
|
Характерними відмовами машин є:
|
• відмови, які зумовлені зміною розміру та геометричної
форми деталі;
• відмови внаслідок зниженням
міцності деталі;
• відмови внаслідок природного
(фізичного) зносу.
|
Природний (фізичний) знос виникає внаслідок:
|
• механічних процесів (механічний знос);
• стомлювального руйнування
(стомлювальний знос);
• хімічних процесів
(корозійний знос);
• теплових процесів (тепловий
знос);
• погіршення фізико-механічних
властивостей матеріалу деталей (пружності, міцності, теплопровідності).
|
Механічний знос, у свою чергу, проявляється у двох формах: зносів тертя (рис. 1.6) і
тиску (рис. 1.15). Машини (крім фізичного зносу) піддаються так званому
моральному (економічному) зносу.
Моральним зносом називають зменшення вартості машин (складальної одиниці) під впливом
науково-технічного прогресу. Моральний знос буває першого і другого родів.
Моральний знос першого роду характеризується втратою вартості діючих машин у
міру того, як відтворення такої ж конструкції машин дорожчає. Моральний знос
другого роду характеризується втратою вартості машин внаслідок виникнення
більш досконалих його типів.
Фактори, що спричиняють несправності машин, поділяють на: конструктивні, технологічні,
експлуатаційні та ін.
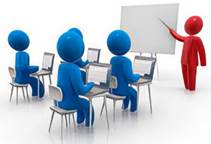
|
Конструктивні фактори, що спричиняють несправності
визначаються:
|
• зміною форми і розмірів
деталей;
• порушенням жорсткості конструкції
(тобто властивістю деталей, особливо базових деформуватися під дією
навантажень, що сприймаються;
• невідповідною точністю
взаємного розміщення поверхонь та осей спільно працюючих деталей;
• не правильним вибором посадок, які забезпечують надійну
роботу спряжень тощо.
|
Технологічні фактори, що спричиняють несправності
визначаються:
|
• порушенням точності
виготовлення деталей;
• не відповідний вибір якості
матеріалу деталей;
• порушенням режимів обробки
деталей;
• не належною якістю
складальних робіт тощо.
|
Експлуатаційні фактори, що спричиняють несправності
визначаються:
|
• погіршенням дорожніх і
кліматичних умов (найбільше впливають на технічний стан машин);
• порушенням міцності дорожніх
покриттів.
|
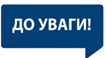
|
Суттєво впливають на факт виникнення несправностей
умови експлуатації машин. Прискорюють час виникнення несправностей
нехарактерні для нормальних умов експлуатації динамічні навантаження в
деталях і механізмах машин. Наприклад, під час систематичного різкого
вмикання зчеплення крутний момент, що передається до трансмісії, може
спричинити виникнення несправностей в механізмах.
|
Важливу роль
для зниження інтенсивності спрацювання і підвищення придатності до
експлуатації більшості деталей відіграє зменшення сил тертя. Зокрема, за рахунок
мащення пар тертя. Отже, для забезпечення довговічності роботи важливим є
своєчасне і якісне проведення ТО та діагностування машин.
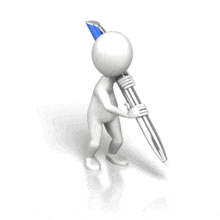
|
Заходи щодо зменшення спрацювання:
|
• застосування
паливно-мастильних матеріалів, що вказані у заводських інструкціях;
• підбір кваліфікованих
кадрів;
• нанесення на поверхню
деталей твердих покриттів;
• ретельна механічна обробка,
що відповідає точності розмірів;
• своєчасне виконання рекомендованого
переліку регламентних робіт з технічного обслуговування.
|
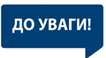
|
Зменшення спрацювання в часі досягається дотриманням
технічних умов на складання, обкатку і випробування та контроль якості
обслуговування і ремонту.
|
|